[Interdisciplinary] [Civil Engineering] [Chemical Engineering] [Electrical Engineering] [Mechanical Engineering]
2024 CAPSTONE PROJECTS
[Interdisciplinary] [Civil Engineering] [Chemical Engineering] [Electrical Engineering] [Mechanical Engineering]
2023 CAPSTONE PROJECTS
[Interdisciplinary] [Civil Engineering] [Chemical Engineering] [Electrical Engineering] [Mechanical Engineering]
MECHANICAL ENGINEERING CAPSTONE PROJECT ARCHIVES
[2022] [2021] [2020]
2022 CAPSTONE PROJECTS
SOLAR DECATHLON:
THE FREEDOM VILLAGE
KEVIN DAI
ADVISED BY PROFESSOR MELODY BAGLIONE
Buildings contribute almost 70% of greenhouse gas emissions in New York City. In addition, this city has been facing an affordable housing crisis for decades with more than 60,000 New Yorkers sleeping in homeless shelters every night, a disproportionate amount being victims of domestic violence or individuals with disabilities. The Cooper Union’s interdisciplinary Solar Decathlon team has been collaborating on The Freedom Village Project, currently being developed by Barrier Free Living to provide temporary and permanent housing for survivors of domestic violence with disabilities. The mechanical design will incorporate variable refrigerant flow and ductless heat recovery ventilation to reduce heating and cooling loads while providing optimal occupant comfort. An energy model was simulated using OpenStudio EnergyPlus to correctly size equipment and estimate the overall energy use.
LINK TO CONTENT

VR HAPTICS:
TOUCING A VIRTUAL WORLD
Yongjun Kim
Sungmin Choi
Justin Hoey
ADVISED BY PROFESSOR ROBERT DELL
VR HAPTICS:
TOUCING A VIRTUAL WORLD
Yongjun Kim
Sungmin Choi
Justin Hoey
ADVISED BY PROFESSOR ROBERT DELLWhen experiencing virtual reality, current consumer headsets provide stereoscopic video and binaural audio to recreate a virtual environment for the user. An important component of a VR system is the controllers, which allow the user to interact and influence the digital world beyond shaking their head. Current consumer VR Controllers inhibit the user’s ability to interact with the virtual world, as every object they grab feels the same: a smooth, uniformly sized plastic cylinder.
Our project seeks to provide a low cost solution by using simple ratcheting joints over the fingers to stop the user’s grip when their fingers contact a virtual object. These joints will be mounted to a 3D printed exo-frame around the user’s hand. To stop a user’s fingers in the desired position, electromagnets engage the finger seizing mechanisms for each individual joint. This allows us to simulate a variety of different shapes, and therefore allows the user to hold and distinguish between cubes, spheres, and cylinders.
LINK TO CONTENT

HUMAN POWERED VEHICLE
Jeannette Circe
Dongjun Kim
ADVISED BY PROFESSOR SVEN HAVERKAMPOur project is to design an alternative transportation method that is human powered. By designing a recumbent tricycle with two wheels in the front, our vehicle is pedal-powered, steerable, stoppable, stable, and safe. Our first prototype has a fixed gear ratio, flat frame design, disc brakes, direct steering, and an adjustable pedal system to accommodate drivers of all heights. We hope that future Cooper Union students can build upon our design to compete in the American Society of Mechanical Engineer’s international competition with more complex elements such as suspension, rollover protection beams, or an electric energy storage component.
LINK TO CONTENT

H2Go: WATER POWERED CART
Brandon Ho
Josh Yoon
J. Jacobowitz
ADVISED BY PROFESSOR DAVID WOOTTON
This year’s ASME Student Design Competition, titled “H2Go”, challenged students to design a water-powered, remote-controlled transportation device. Teams were tasked with implementing an efficient method of converting the potential energy of water into useful energy to drive the device across the playing field, transporting as much water as possible within the given time limit. Points were awarded based on the quantity of water transported, with bonus multipliers for performing extra tasks or for having a highly-rated design. To generate electrical energy, we manufactured a custom alternator from 3D-printed parts, neodymium magnets, and magnet wire. To spin our alternator, we directed a jet of water at a 3D-printed Pelton turbine. The energy was stored in a super-capacitor bank and was used to power two low-voltage DC motors when controlled by the Bluetooth-connected smartphone app. The design cycle focused on refinement, resulting in improvements such as tripling the drive distance through redesigning the motor controllers and altering the flow system to reduce the charging time by 48 percent. The design scored 2nd out of 17 in the competition.
LINK TO CONTENT
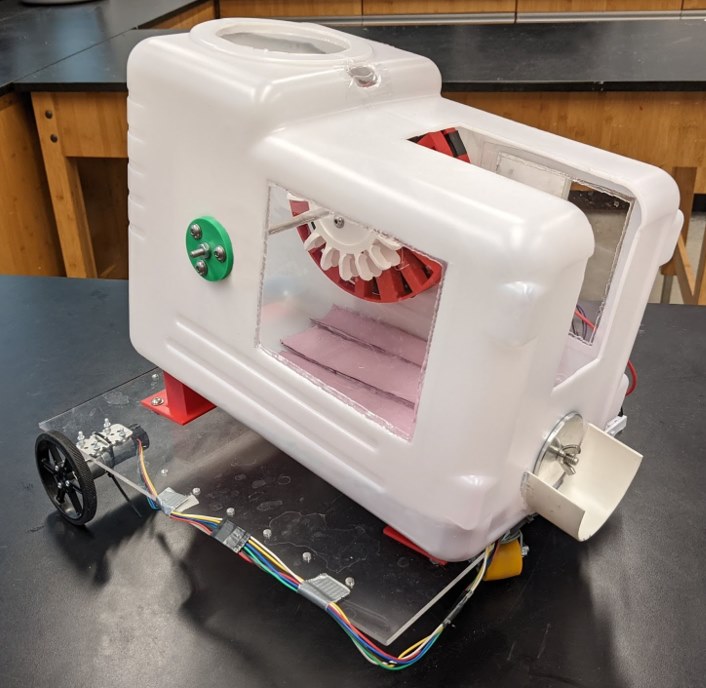
SOFT ROBOTIC GRIPPER
Anthony Chen Alexander Koldy
Solbi Oh
Robotic grippers have the potential to be used for complex task completion within people’s homes. Traditional grippers are typically composed of hard materials and parts, such as metal and motors, making them potentially unsafe for a home environment. In order to bring robots to homes, extra attention must be given to safety by making grippers soft and compliant. Silicone-based soft robotic grippers show promise in solving this issue, however, they lack the dexterity and precision of traditional hard grippers; Completion of complex home tasks like cooking using soft robotics is currently not possible. Our project is aimed at the design and control of soft grippers which have multiple individually-actuated sections of bend, mimicking the dexterous design of a human hand. This involves the use of rapid iterative silicone molding processes and the creation of a custom “bang-bang” control scheme.
LINK TO CONTENT
LINK TO CONTENT


